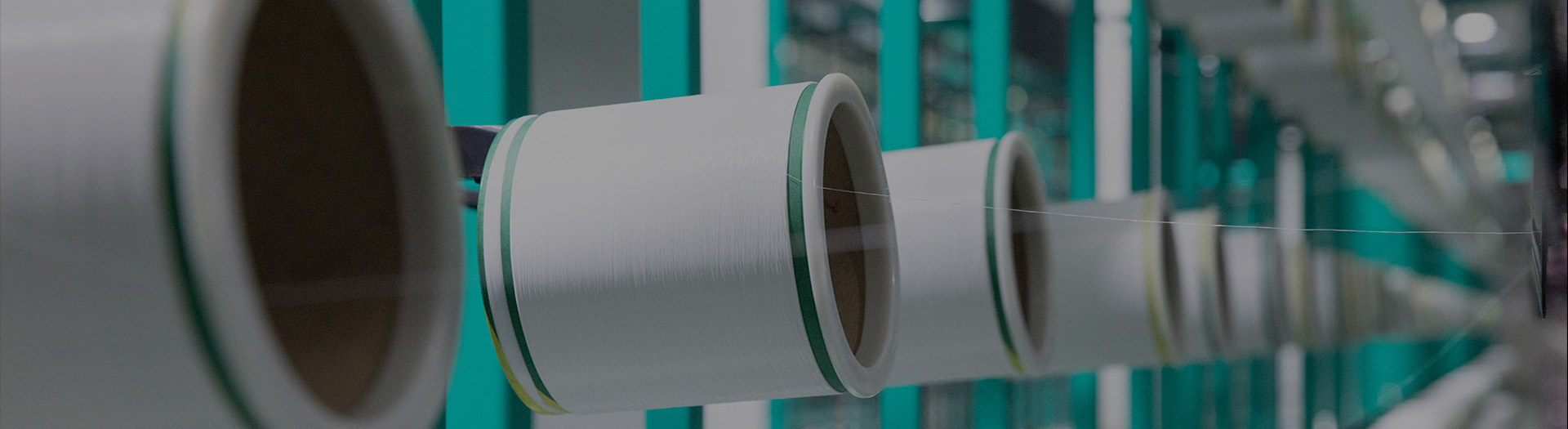
BLOG
What Makes Polyamide Chips 6 Ideal for High-Temperature Applications?
Polyamide chips 6, a key material derived from Nylon 6, are rapidly gaining attention in various industries due to their remarkable properties and versatility. Known for their strength, durability, and ability to withstand high temperatures, these chips are crucial in a variety of applications, from packaging to automotive parts. In this blog, we will explore the benefits and unique features of polyamide chips 6, particularly in high-temperature applications, and how they are transforming the manufacturing processes in diverse sectors.
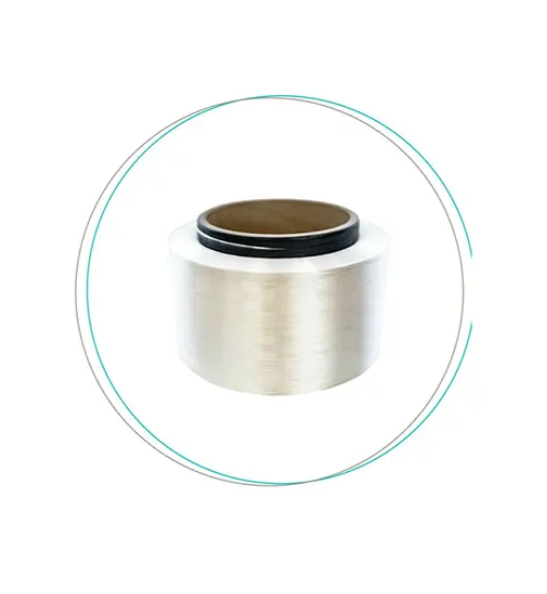
What Makes Polyamide Chips 6 Ideal for High-Temperature Applications?
Polyamide chips 6 are widely recognized for their superior thermal stability, making them ideal for high-temperature environments. Unlike other polymers, polyamide 6 exhibits exceptional resistance to heat, which is a critical factor for applications that involve exposure to elevated temperatures. Whether it’s in automotive engines, industrial machinery, or electrical components, polyamide chips 6 maintain their structural integrity even under challenging thermal conditions.
The reason polyamide chips 6 excel in high-temperature settings lies in their molecular structure. The material has a high melting point compared to other polymers, which helps prevent deformation or breakdown under heat stress. Additionally, polyamide 6 has a relatively low coefficient of thermal expansion, which means it resists changes in size when exposed to temperature fluctuations. This stability is essential for ensuring the performance and longevity of components in industries such as automotive, aerospace, and electronics.
Polyamide Chips 6 in the Packaging Industry: Strength, Flexibility, and Cost Efficiency
Polyamide chips 6 have found significant applications in the packaging industry, where strength, flexibility, and cost efficiency are essential. Packaging materials made from polyamide 6 are not only durable but also lightweight, making them ideal for creating high-performance packaging solutions. Polyamide chips 6 offer excellent barrier properties, protecting the contents from moisture, air, and contaminants, which is crucial for maintaining product freshness and integrity.
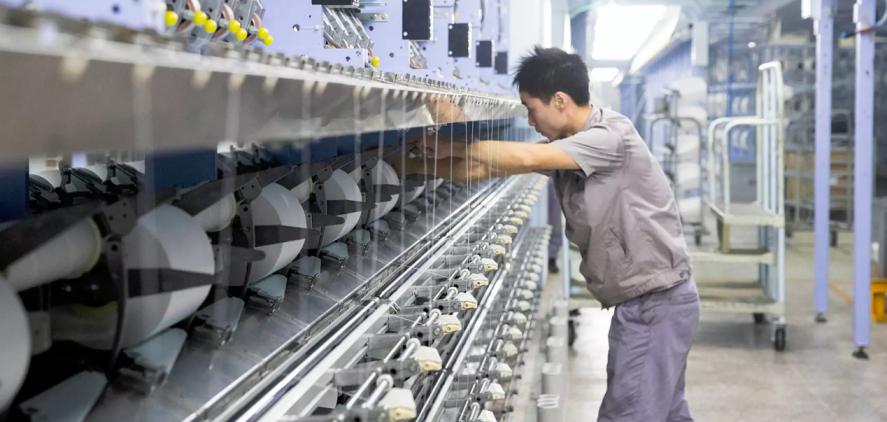
One of the key benefits of polyamide chips 6 in packaging is their flexibility. The material can be molded into various forms, from films and bags to rigid containers, allowing manufacturers to create packaging solutions that meet a wide range of functional requirements. Moreover, polyamide 6 is highly resistant to abrasion and puncturing, ensuring that packaged goods remain safe during transportation and storage.
In addition to performance, cost efficiency is a major advantage. Polyamide chips 6 are relatively affordable compared to other high-performance plastics, allowing manufacturers to produce cost-effective yet reliable packaging solutions. This balance of strength, flexibility, and cost-effectiveness is why polyamide 6 is increasingly being used in both consumer goods and industrial packaging.
The Benefits of Polyamide Chips 6 in Manufacturing Lightweight Automotive Parts
The automotive industry is another major beneficiary of polyamide chips 6, which are increasingly used in the production of lightweight automotive parts. In an era where reducing vehicle weight is essential for improving fuel efficiency and reducing carbon emissions, polyamide chips 6 play a crucial role. These chips can be molded into complex shapes and structures, making them ideal for producing components that are both lightweight and durable.
Polyamide 6 offers high strength-to-weight ratios, meaning that automotive parts made from this material can be both strong and lightweight. This is especially important for parts such as engine components, transmission systems, and interior trims. By replacing heavier metal parts with polyamide 6, automakers can significantly reduce the overall weight of the vehicle without compromising on performance or safety.
Additionally, polyamide 6’s resistance to heat, chemicals, and wear makes it ideal for automotive applications that require high-performance materials. Whether it’s under-the-hood components or exterior parts exposed to harsh environmental conditions, polyamide chips 6 provide the durability needed for long-lasting automotive parts.
Polyamide Chips 6 vs. Polypropylene: Which One Is Better for Your Project?
When considering materials for a specific application, many manufacturers face the decision of choosing between polyamide 6 and polypropylene (PP). While both materials offer benefits in various industries, polyamide chips 6 generally outperform polypropylene in several key areas.
Polyamide 6 has superior mechanical strength, making it ideal for applications that require high load-bearing capacity. It is also more heat-resistant than polypropylene, which makes it a better choice for applications that involve high-temperature environments. Additionally, polyamide 6 has better chemical resistance, making it more suitable for automotive, industrial, and packaging applications where exposure to oils, fuels, and other harsh chemicals is common.
On the other hand, polypropylene is a more affordable material and offers excellent resistance to moisture. However, it lacks the high-strength and high-temperature capabilities of polyamide 6. Therefore, for projects requiring toughness, durability, and the ability to perform under elevated temperatures, polyamide 6 is generally the better choice.
Exploring the Environmental Impact of Polyamide Chips 6 and Their Sustainability
As sustainability becomes an increasingly important factor in manufacturing, the environmental impact of materials like polyamide chips 6 is drawing more attention. While polyamide 6 is derived from petrochemical resources, efforts are underway to develop more sustainable production methods. For example, polyamide 6 can be recycled, which reduces the material’s overall environmental footprint. Recycling polyamide 6 reduces the need for new raw materials, cutting down on energy consumption and waste.
Moreover, polyamide 6 has the potential to be produced using renewable resources. Some manufacturers are already experimenting with bio-based feedstocks, which could make polyamide 6 a more eco-friendly alternative to traditional plastics. The material’s durability and long lifespan also contribute to its sustainability, as products made from polyamide chips 6 often have a longer service life, reducing the need for frequent replacements.
The use of polyamide 6 in industries such as automotive and packaging can also contribute to sustainability goals. For instance, lighter automotive parts reduce fuel consumption and CO2 emissions, while efficient packaging solutions minimize waste and improve the shelf life of products.
Premium Nylon 6 FDY Yarn: Enhanced Performance and Versatility
One of the key products derived from polyamide chips 6 is Nylon 6 FDY (Fully Drawn Yarn), which is produced by fully drawing Nylon 6 fibers to create a stronger, more durable yarn. Nylon 6 FDY is a versatile material used in various textile applications, such as fishing nets, ropes, automotive parts, and industrial fabrics.
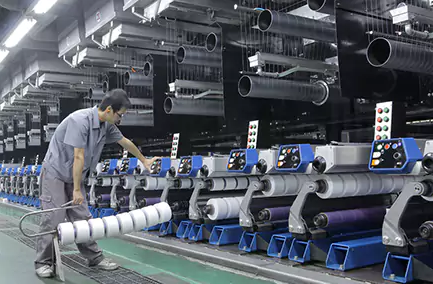
The advantages of Nylon 6 FDY include its lower melting point, which allows for better adhesion during the yarn manufacturing process. It is also known for its excellent warmth retention, making it ideal for use in thermal wear and insulating textiles. Additionally, Nylon 6 FDY reflects far infrared rays, improving blood circulation and providing health benefits when used in functional and therapeutic textiles.
Nylon 6 FDY’s durability and resistance to wear and tear make it perfect for high-performance fabrics that need to withstand harsh conditions, from industrial environments to outdoor sports applications. Whether it’s for functional wear, home textiles, or industrial fabrics, Nylon 6 FDY provides the toughness and flexibility needed for demanding applications.
Conclusion: Why Polyamide Chips 6 Are a Game-Changer for Modern Manufacturing
Polyamide chips 6 from Hochsonne are quickly becoming an essential material across various industries due to their outstanding performance characteristics, including high strength, heat resistance, and durability. From high-temperature applications to packaging, automotive, and textile production, polyamide chips 6 are revolutionizing the way products are manufactured.
As the demand for sustainable materials increases, polyamide 6 is also evolving to meet environmental concerns, with innovations in recycling and bio-based production methods. Whether you are looking to create lightweight automotive parts, durable packaging, or high-performance textiles, polyamide chips 6 offer the perfect combination of strength, flexibility, and cost-efficiency.
For businesses looking to source high-quality polyamide chips 6, Hochsonne, a leading supplier, offers premium-grade materials that meet the needs of modern manufacturing. With a fast delivery time and flexible payment options, Highsun ensures that manufacturers can access the materials they need to stay competitive in today’s fast-paced market.
LASST UNS GEMEINSAM REDEN
Der Kunde ist sehr zufrieden, Ich werde vom Fat Isicing-Entwickler gefolgt, aber der Mutterleib soll in einer solchen Zeit durchtrennt werden, dass