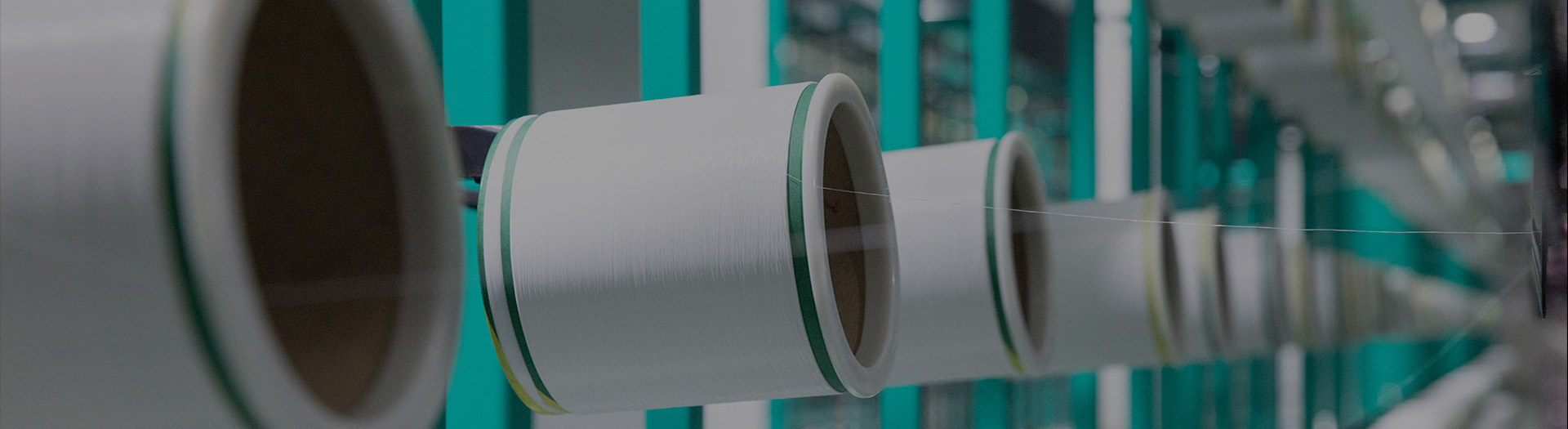
블로그
Advanced Nylon 6 Chips Manufacturing Process: A Dive Into
Have you ever wondered how the versatile fabrics that grace your wardrobe start their life? The journey often begins with something as unassuming as nylon 6 chips. These small but mighty pieces are crucial in the production of everything from clothing to industrial materials. In this blog, we’ll unravel the fascinating manufacturing process of nylon 6 chips, focusing on their significance, features, and the innovative methods employed by manufacturers like Highsun Holding Corporation.
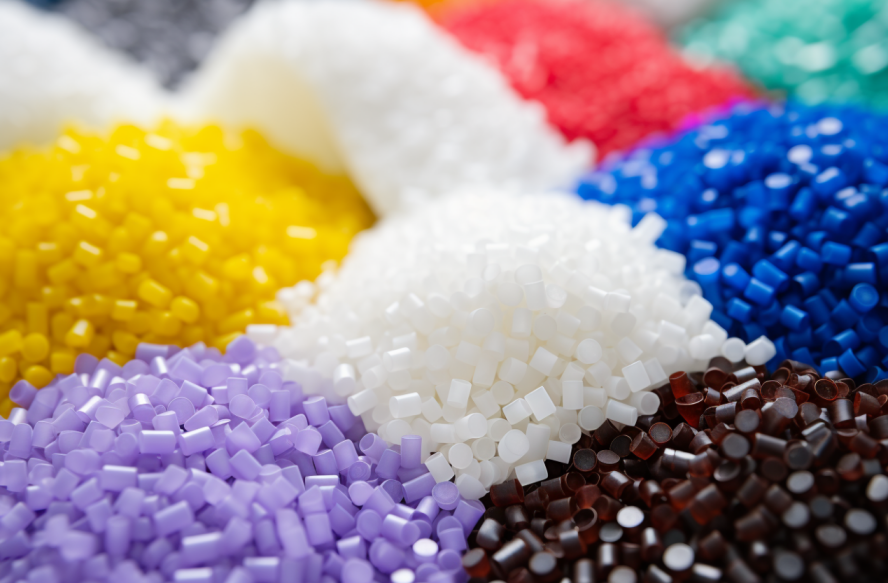
Understanding the Market Landscape
The synthetic chemical fiber industry is experiencing significant growth, driven by increasing demand across various sectors, including textiles, automotive, and industrial applications. Specifically, the nylon 6 chips market is poised for robust expansion. Below is the most recent data illustrating the market size and growth projections:
Year | Market Size (USD Billion) | Compound Annual Growth Rate (CAGR) | Projected Market Size in 2028 (USD Billion) |
2023 | 5.5 | 5.2% | 7.3 |
Market Insights
The Nylon 6 Chips Market is expected to be valued at approximately USD 5.5 billion in 2023. This reflects the growing importance of synthetic fibers in manufacturing and everyday products. The projected compound annual growth rate (CAGR) ~이다 5.2%, indicating strong demand trends. It is expected to reach approximately USD 7.3 billion by 2028. This growth is fueled by advancements in textile technologies and an increasing shift toward sustainable materials.
Driving Factors
Several factors contribute to this growth trajectory. The versatility of nylon 6 chips, along with their superior strength and durability, makes them an ideal choice for a variety of applications. 뿐만 아니라, innovations in production processes and a focus on sustainability are enhancing their appeal in the market.
What Are Nylon 6 Chips: The Building Blocks of Fabrics
What Are Nylon 6 Chips?
나일론 6 chips are small plastic pellets made from caprolactam, a type of synthetic polymer. They are the raw materials for producing nylon fibers and fabrics. Nylon fibers and fabrics are known for their strength, elasticity, and durability. Unlike other types of nylon, 나일론 6 is produced through a process called ring-opening polymerization. This makes it unique in the textile industry.
The Role of Titanium Dioxide (TiO2)
One of the defining features of nylon 6 chips is their finish, which is influenced by the titanium dioxide (TiO2) 콘텐츠. The different finishes—Bright, Semi-Dull, and Full-Dull—are formulated to meet various aesthetic and functional needs. The TiO2 content affects color, opacity, and overall appearance, enabling manufacturers to tailor products to specific requirements.
Applications in Textile Manufacturing
나일론 6 chips are not just versatile in appearance; they are equally functional. These chips find their way into various textile applications, from everyday clothing to high-performance industrial materials. Their adaptability makes them a go-to choice for manufacturers looking to create both decorative and functional fabrics.
나일론 6 Chips Manufacturing Process: From Caprolactam to Chips
Step 1: Raw Material Procurement
나일론 6 Chips Manufacturing Process Step 1 — The manufacturing of nylon 6 chips begins with the procurement of caprolactam, the primary raw material. Caprolactam is produced through a chemical process involving cyclohexanone and ammonia. This first step is crucial, as the quality of caprolactam directly influences the quality of the final nylon 6 chips.
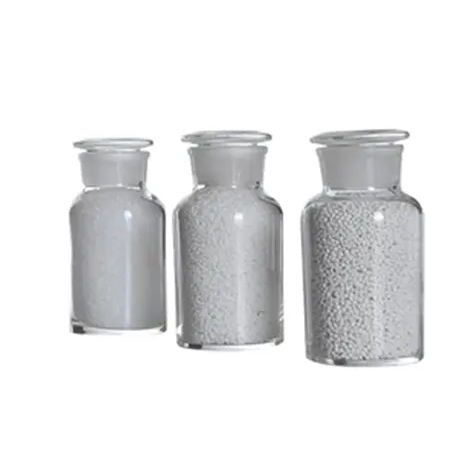
Step 2: Polymerization
나일론 6 Chips Manufacturing Process Step 2 — Once the caprolactam is secured, the next phase is polymerization. During this process, caprolactam undergoes ring-opening to form long chains of nylon 6. This step requires precise temperature and pressure controls to ensure a consistent molecular weight, which is vital for the performance characteristics of the nylon 6 chips.
Step 3: Cooling and Granulation
나일론 6 Chips Manufacturing Process Step 3 — After polymerization, the nylon is cooled and solidified. It is then broken down into smaller, manageable pieces through a process called granulation. This step transforms the solid nylon into the small chips used in fabric production, ensuring uniform size and quality.
The Finishing Touches: Achieving Different Aesthetics
Bright Finish (BR)
The Bright finish nylon 6 chips are characterized by their luminous translucency, achieved through a 0% TiO2 content. This finish is perfect for applications that require high transparency and brightness, making it an ideal choice for lightweight fabrics and technical textiles.
Semi-Dull Finish (SD)
With a TiO2 content of 0.3%, the Semi-Dull chips offer a milk-white appearance that strikes a balance between brightness and opacity. This finish is versatile and is often used in apparel where a softer, less reflective look is desired, catering to both aesthetic and functional requirements.
Full-Dull Finish (FD)
Full-Dull nylon 6 chips, containing approximately 1.6% TiO2, provide a subdued, beige white color. This matte finish is favored in applications that demand a non-reflective surface, such as upholstery and industrial fabrics, enhancing the practicality and versatility of the final product.
하이선: Pioneering Nylon 6 Chip Production
A Legacy of Excellence
설립연도 1984 in Fujian, 중국, Highsun Holding Corporation has become a leader in the synthetic chemical fiber industry. With over 8,000 직원과 21 affiliates globally, Highsun is dedicated to providing high-quality nylon 6 chips and other chemical fibers. Their commitment to quality has allowed them to collaborate with 25 of the world’s top 500 companies, establishing a strong reputation in the industry.
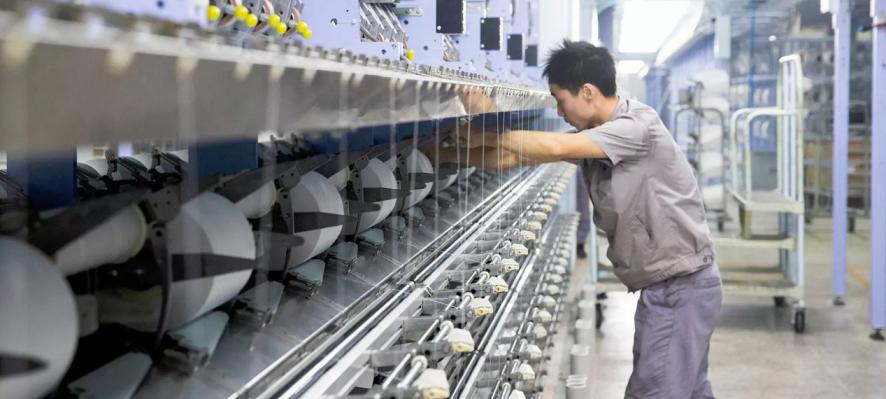
Comprehensive Industrial Chain
Hishen’s success is due to its complete industrial chain solutions. Covering every step from cyclohexanone to dyeing and finishing. This integrated model not only ensures product quality and sustainability. And it can be delivered in time to meet the different needs of customers around the world.
Innovation and Sustainability
As a modernized enterprise, Highsun places a strong emphasis on innovation and sustainability in its manufacturing processes. By leveraging cutting-edge technology and environmentally friendly practices, the company aims to reduce its carbon footprint while maintaining high product standards.
결론: The Future of Nylon 6 Chips
The manufacturing process of nylon 6 chips is very complex. It starts with the raw materials and ends up with a multifunctional product that plays a key role in modern textiles. From various surface treatments to functional applications. 나일론 6 chips are essential to create the fabrics that shape our lives.
As manufacturers like 하이선 continue to innovate and expand their capabilities, the future of nylon 6 chips looks promising. With a focus on quality, 지속 가능성, and adaptability, the nylon 6 chips manufacturing process is set to meet the evolving demands of the textile industry for years to come.
LET'S TALK TOGETHER
고객은 매우 행복합니다, 팻아이싱 개발자 따라오겠습니다, 하지만 그런 시기에 자궁을 자르게 놔두세요.